The importance of standards in a digital world
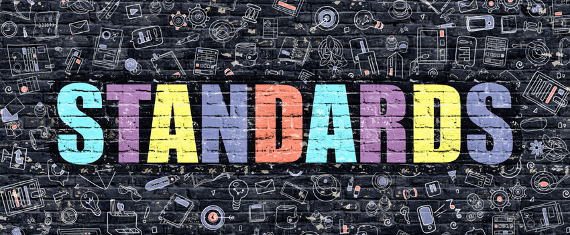
With many of the benefits of digital manufacturing arising from data gathering and collaborative working across supply chains, developing standards and open architectures will have a major part to play in making the digital future a reality. Currently, the definitions of key terms are hugely variable within sectors let alone the mechanisms for data capture and analysis. Providing standards and establishing good practice will be fundamental to a data-driven, digitally-connected world.
In order to help it develop a clear understanding of how it can best support manufacturers, BSI asked the IfM’s dissemination arm, IfM ECS, to bring together a group of researchers from IfM, Cranfield University and the University of Nottingham. The aim of the project was to understand the opportunities, benefits, challenges and barriers for manufacturing and to outline the areas where standards and good practice can make a difference. The findings have been published by IfM ECS in a report: Application of digital technologies to innovation in manufacturing.
The manufacturers’ view
The team carried out a survey of UK manufacturers to build up a picture of how important they perceive digitalisation to be, where the benefits will emerge and what are the key competences needed across the value chain.
Increasing productivity was seen as one of the major prizes – both for individual companies and for the UK as a whole. Better customer service was also perceived to be an important outcome that would derive from a combination of digital capabilities: the personalisation of products and services, smarter and faster service, lower costs, higher quality and more widespread availability. These benefits were seen as arising from flexible manufacturing, ‘mass customisation’ and value chain optimisation.
Digital manufacturing holds out the prospect of many opportunities, therefore, but part of the challenge is being able to see which of them are most likely to be realised in the short and medium term – and which will create the most value for companies. The two opportunities which manufacturers scored most highly were flexible manufacturing and value chain optimisation. The benefits of these were linked – both relating largely to better control and management through greater visibility and access to information.
While the consensus is that digital manufacturing is going to play a vital part in supporting a sustainable manufacturing sector in the UK, there is also a recognition that moving towards digital manufacturing is slow-going. Why is that?
Two types of challenge
The report breaks down the challenges into two broad categories: organisational and technical or logistical. Among the organisational challenges there is a sense that although the cost of adopting digital technologies is a real and significant barrier, a lack of vision and the absence of a ‘digital mind-set’ amongst senior executives is also contributing to the problem. Skills shortages – a perennial problem for advanced manufacturing in the UK – are even more acute in this context. The digital world provides the infrastructure for companies to work together to deliver better solutions but the companies aren’t necessarily ready to embrace more collaborative ways of working.
Risky business
Security is also a very real concern for many companies who recognise the risk but aren’t sure either how to quantify it or address it. Other risks are associated with digital manufacturing. Increased automation, for example, means that robots and humans will be increasingly sharing work spaces. What are the health and safety implications of that scenario?
Distributed digital manufacturing also poses new questions for quality control. In the conventional manufacturing model, if production is outsourced to a third party
there are processes in place to monitor the quality of the product build. In the new digital world, the production company will receive a design and manufacture specification which can be easily adapted. Standards will need to be developed to ensure that any variance from the original specification is fully traceable.
The importance of standards
One of the main areas of challenge was around collaboration and data-sharing. This is an area which can be supported by the development of standards.
Currently, the use of standards for digital manufacturing varies enormously by sector. Aerospace, for example, already has a large number of standards relating to digital manufacturing but it’s a very different story in other sectors. Many companies are only working to their own in-house standards at worst and at best to standards that relate to their own sector. Manufacturers feel that there is a lack of transparency and a need for greater integration.
Priorities
Of the top priorities for getting digital manufacturing moving, number one is skills and training. Second is developing new, digitally-enabled, service-oriented business models. Respondents also called for governance and processes which ‘have vision’ but which are also straightforward to implement. The other key area is developing appropriate cross-sector policies, regulations and light touch standards to support integrated supply chain development, particularly as there will be more requirements to include digital data management in contracts and procurement.
Interoperability vs security
If the potential benefits of digitalisation are to be realised, collaboration will be key. This will be enabled by the interoperability of both machines and data which, in turn, needs open systems, architectures and common languages and data platforms. These are not yet fully developed so companies are forced to develop ‘bespoke’ bridges or interfaces between machines. But this in turn reinforces the need for more secure and resilient manufacturing systems and cross-enterprise digital security systems.
What next?
Developing a set of standards is clearly going to have a critical role to play if the UK is to realise its digital potential. And the report emphasises the importance of the task: “If the UK does not respond within five years, it will lose out to overseas competitors: a concerted, urgent, action programme is needed.”
It calls for the development of a national steering arrangement for digital manufacturing standards – led by key industrial, academic and institutional stakeholders – to ensure that there is a clear vision in policy setting.
IfM Review Issue 6 Articles
Digital Manufacturing at the IfM
The digitalisation of manufacturing economies
How bright is your digital future?
The importance of standards in a digital world
Manufacturing leadership in the age of digital disruption
Find us on
Date published
8 December 2016