The digitalisation of manufacturing economies
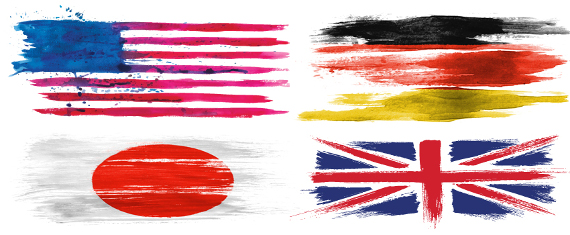
New digital technologies are radically changing the ways firms manufacture products, the business models they adopt, and even how they innovate. At a national level, digital technologies promise to reshape national manufacturing systems and redefine sources of competitive advantage. For governments around the world, this Fourth Industrial Revolution offers opportunities and challenges in key policy areas such as employment, productivity, competitiveness and sustainability.
Dr Eoin O’Sullivan, Head of the IfM’s Centre for Science, Technology and Innovation Policy, reflects on different policy perspectives, priorities and initiatives in the key manufacturing economies – USA, Germany and Japan – and considers the implications for the UK. Dr Eoin O’Sullivan, Head of the IfM’s Centre for Science, Technology and Innovation Policy, reflects on different policy perspectives, priorities and initiatives in the key manufacturing economies – USA, Germany and Japan – and considers the implications for the UK.
Policymakers around the world are taking a keen interest in digital manufacturing for a number of reasons. They see its potential for enhancing productivity and economic growth, for (re)connecting manufacturing and innovation and for creating entirely new markets based on new products and services. Digitalisation also has the potential to improve resource efficiency and therefore help with costs, supply constraints and the sustainability of natural resources. But alongside opportunities lie challenges. Digitalisation has implications – both good and bad – for manufacturing jobs in high-wage economies. It brings with it significant concerns about the cyber security of industrial systems and utilities. And it threatens to disrupt business models in important sectors of the economy, offering opportunities for international competitors to gain market share.
Three dimensions of digital transformation
One of the most striking aspects of the ‘digitalisation of manufacturing’ is the variety both of the language used to describe it and the policy programmes designed to support it. This is, perhaps, unsurprising given the complexity of the technologies and manufacturing systems involved. The convergence of ‘cyber-physical systems’, the ‘internet-of-things’ and ‘big data’ technologies, among others, offer a variety of ways to connect and integrate ever more complex manufacturing supply chains and production systems. Equally, unsurprisingly, different aspects of these systems are more relevant for particular national manufacturing strengths and weaknesses – and for policy challenges where governments have different priorities.
A useful way of cutting through these variations in terminology is by framing the discussion in terms of three manufacturing ‘dimensions’: the vertical integration of flexible and reconfigurable manufacturing systems within businesses (often discussed in terms of ‘smart factories’ or ‘smart manufacturing enterprises’); the horizontal integration of inter-company value chains and networks (or ‘smart supply chains’); and the product lifecycle integration of digital end-to-end engineering activities across the entire value chain of a product and the associated manufacturing system.
There is a growing realisation among policy makers that the ‘digitalisation of manufacturing’ is not just about advanced automation and ‘smart factories’ but needs to embrace all of these three dimensions. These dimensions also provide a useful lens through which to understand the genesis of particular national innovation priorities and policy emphases, some examples of which are outlined below.
Different national approaches
Different governments are using a range of mechanisms and initiatives to address the opportunities and challenges of the digitalisation of manufacturing. While the following examples, from the US, Germany and Japan cannot represent the full breadth and variety of programmes in each country, they do highlight some key national priorities and some important flagship initiatives.
USA
One of the most high profile initiatives in the United States is the Digital Manufacturing & Design Innovation Institute (DMDI) based in Chicago. DMDI is one of the new Manufacturing USA innovation institutes (similar to UK Catapults) with a mission to develop and demonstrate new digital manufacturing and design capabilities in advanced analysis, intelligent machining and advanced manufacturing enterprise. DMDI has 190 member companies, as well as partners from universities and other organisations and funding of $320 million ($70 million of which comes from the government). DMDI’s research agenda is often explained in terms of the so-called ‘digital thread’, an important concept within US thinking about the digitalisation of manufacturing. The term reflects an integrated approach to managing information related to a particular product (or asset) ‘woven’ throughout its lifecycle – a ‘supply chain of data’ from design to manufacturing to product-support.
Many research and innovation activities related to the ‘digital thread’ involve efforts to integrate data from different, traditionally siloed, functional engineering perspectives by developing protocols, information-exchange methods, tools and standards. A complete two-way ‘digital thread’ should enable manufacturing firms to deal more effectively with the complexity of modern products and manufacturing systems, reducing cycle times and increasing productivity and competitiveness.
Germany
In digital manufacturing terms, Germany is most associated with Industry 4.0 and its emphasis on smart factories and smart manufacturing enterprises. But it also attends to that other source of German manufacturing strength – small and medium sized enterprises.
One of the most high profile investments of the Federal Government’s Industry 4.0 initiative is the ‘It’s OWL’ (Intelligent Technical Systems OstWestfalenLippe) cluster. It’s OWL is an alliance of over 170 businesses, universities and institutes in OstWestfalenLippe – a region with a number of industrial and research strengths. The alliance is funded through the Leading-Edge Cluster program which supports top-performing commercial and scientific clusters. It’s OWL has received over €100 million over five years, funding 46 research projects to develop intelligent technical systems. While it has a significant focus on research, the cluster is also very much concerned with helping SMEs develop their capabilities.
Japan
The Japanese government’s most recent review of manufacturing highlights that, although Japan is adopting the ‘Internet of Things’, it may have fewer value capture
opportunities than the United States or Europe. The US has opportunities to capture value particularly through internet platforms and big data analysis (through firms like Google) and Germany has opportunities related to the connectivity of production machines and smart factories, through firms like Siemens. Japan, on the other hand, is comparatively strong in advanced robotics and its government has prioritised efforts to lead the world in ‘robots for the Internet-of-Things era’. The Japanese Robot Revolution Council Initiative, backed by over 200 companies, universities and research institutes, aims to expand the use of advanced robotics throughout Japanese industry, with the aim of growing sales from ¥600 billion a year to ¥2.4 trillion a year (roughly £19 billion a year) by 2020.
... it is worth noting that many national priorities for the digitalisation of manufacturing build on long-standing national industrial strengths and established national manufacturing capabilities.
Although most major economies have research and innovation efforts related to the digitalisation of manufacturing, there are, then, significant variations in emphasis and perceived opportunities. The US has, perhaps, a greater emphasis on the opportunities associated with new product design (and speed to market) and the knowledge management enabled by ‘big data’. Germany has a relatively stronger emphasis on ‘embedded systems’ and the ‘smart factories’ of the future. Japan has identified national opportunities in cyber physical systems and ‘advanced robotics for the ‘Internet of Things’ era. These are all new opportunities enabled by new ICT and manufacturing technologies, but it is worth noting that many national priorities for the digitalisation of manufacturing build on long-standing national industrial strengths and established national manufacturing capabilities.
What about the UK?
So what are the implications of the digitalisation of manufacturing for the UK? What are the opportunities (and challenges) given Britain’s existing manufacturing and innovation base?
Britain may not be home to the headquarters of giant global internet firms like Google, or have a ‘Mittelstand’ of manufacturing engineering SMEs like Germany, or have a national tradition and passion for robotics like Japan, but it does have an extremely strong engineering and design base, and a thriving ICT community. And from a policy perspective, the UK has adopted a systematic policy approach to ‘industrial strategy’, which may well be ideally suited to addressing the opportunities and challenges of digitalisation.
In recent years, UK industrial strategy has focused on long-term strategic support of key sectors through the co-ordinated development of skills, technology capabilities, key infrastructure and access to finance. At the same time, flagship initiatives such as the Advanced Manufacturing Supply Chain Initiative and the Catapult network of intermediate R&D centres have an important role to play in enhancing the critical linkages throughout the UK’s innovation and manufacturing systems.
More recently, in July 2016, the Government announced a major overhaul of the UK business ministry, giving it a new name – the Department of Business, Energy and Industrial Strategy – suggesting further commitment to strategic, systematic and joined-up policy-making. This systematic approach will become ever more important as digitalisation continues to transform and integrate manufacturing technologies, systems and supply chains, creating new sector-specific opportunities, but also others that cut across traditional sector boundaries and require common innovation infrastructure, skills and R&D investment.
The levels of international policy interest, investment and urgency, reflect an expectation that digitalisation will radically reshape manufacturing systems, value chains and sources of national competitive advantage.
The policy challenge
For manufacturing economies, policy initiatives related to the digitalisation of manufacturing are, therefore, about much more than just digital technology research and innovation. In particular, there are significant efforts to address market failures related to skills and workforce development, ICT infrastructure, SME capacity-building, as well as standards development, data transparency and trust, IP rights and cyber security.
The levels of international policy interest, investment and urgency, reflect an expectation that digitalisation will radically reshape manufacturing systems, value chains and sources of national competitive advantage. The complexity of digitalised manufacturing systems, the variety of perceived opportunities and challenges, and the different policy approaches to addressing them suggest there is still no consensus on how the ‘Fourth Industrial Revolution’ will play out, how value will be (re)distributed throughout global manufacturing networks, or which capabilities will determine who wins and who loses. The revolution is coming, but there is everything still to play for.
IfM Review Issue 6 Articles
![]() |
Digital Manufacturing at the IfM |
![]() |
|
![]() |
|
![]() |
|
![]() |
|
![]() |