Keeping the supply chain flowing
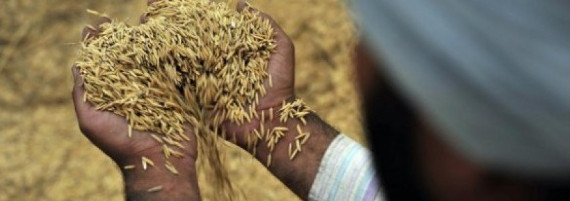
A typical supply chain can be a vast, sprawling network of producers, suppliers, ‘super middlemen’, retailers and consumers that connect, for instance, a piece of mined aluminium with a finished car, or a field of wheat with a loaf of bread on the table.
Dr Jag Srai and the team he heads in the Centre for International Manufacturing like nothing better than a complex, multi-faceted supply chain, because within the connections lies a vital source of competitive advantage. Companies that can more optimally ‘configure’ this complex network have the opportunity not only to improve their business but also to do so sustainably in an otherwise resource-hungry and wasteful world.
“Many supply chains today have developed over time, a consequence of often short-term tactical decisions or ill-considered mergers and acquisitions,” he explains. “There may be large distances between component supply and the end product, delays in sharing information along the chain, or an excessive fragmentation of activities.
“Within little more than a generation, the traditional model of a vertically integrated firm, which has most of its component and final product in-house, has become fragmented. Today, for manufacturing a typical consumer electronics product, dozens of firms in as many countries might be involved in its manufacture, with activities dispersed among narrowly focused companies distributed across developed and emerging economies.”
Srai’s team has been mapping these global networks across multiple sectors, developing novel tools for their visualisation and for identifying opportunities to reconfigure them to meet demand more effectively.
Of particular focus has been a comparison of the food and pharmaceutical process industries, and the assembly power houses of aeronautical and automotive industries, in both the UK and India.
“Manufacturing is a top priority in both countries,” explains Professor Sir Mike Gregory, former Head of the IfM, where the Centre is based. “In the UK, the government has placed manufacturing at the heart of plans for economic recovery. And in India, the government launched the ‘Make in India’ initiative in 2014 with the aim of transforming the country into a major global manufacturing hub and generating millions of new jobs.”
The project is funded by the UK’s Engineering and Physical Sciences Research Council and the Indian Department of Science and Technology. It began a year ago but follows a previous study in which the team created a set of representations of the UK food supply chain for dairy, fruit and vegetables, and staple foods. It was painstakingly collated from industrial reports, literature reviews and first-hand case studies, as well as interviews with key industrial players.
The resulting map provides a fascinating insight into the dynamics of networks that many consumers are unaware of – such as the one that links a cow on a dairy farm to a pint of milk on a UK doorstep (a seven-step process, as it turns out).
Crucially, it also identifies how new trends are being driven by an increasing demand from consumers to know where their food is coming from and for cheaper, own-brand labels. “Organisations that are able to align these complex networks with their own strategic aims have an opportunity to set themselves apart from their competitors,” explains Srai.
One of the researchers’ main interests is how maps such as this can be used to foster a more sustainable approach to manufacturing, as Dr Mukesh Kumar explains: “Food security, for instance, is a global challenge as populations continue to grow, yet 30–40% of food in the UK is currently wasted, mostly at the retail and consumer end of the chain.”
Working with their collaborators in India, the team has now generated comparable maps of the Indian food supply chain. The comparison could help each to explore the key differences and identify how multinationals from one country looking to do business in the other might need to adapt a supply chain to work best.
“The UK food retail chain is dominated by a few large, organised retailers who control 73% of UK grocery sales, and as a result exert considerable influence over upstream partners in the chain, whereas in India this type of organised retail accounts for only 12% of sales,” Kumar explains.
“But the largest difference is where the wastage happens. In India, most wastage occurs at the early stages of the supply chain, with tonnes of fruit and vegetables perishing due to poor handling and storage facilities and lack of cold chain infrastructure.”
According to estimates by the United Nation’s Food and Agriculture Organization, each year about 40% of India’s fresh fruit and vegetables rot before reaching consumers’ plates, as does an amount of wheat almost equal to Australia’s total annual production.
“Supply chains that link the UK and India incur waste up- and downstream. The figures are quite scary – you sometimes wonder how anything ends up on a plate!” observes Srai.
He highlights how crucial it has been to work closely with Indian researchers, industry and policy makers, helped by funding through the UK India Education and Research Initiative: “We have chosen partners in India who complement our skills. It’s like a supply chain in action! It has seen a continuous stream of collaborations emerging out of this, none of which would have been possible without this project.”
For instance, researchers at the Indian Institute of Technology Ropar and the Indian Institute of Management Lucknow have been looking at how simulation and modelling of operations could be used to flag up sustainability challenges.
“Our Centre’s research on ‘network mapping’ tools and close links to industry have meant that we have provided methods and industry contacts to our partners, while leveraging their specialist skills in the specific areas that we require. We have also taken the combined output to inform our wider work in the University’s Strategic Research Initiative on Global Food Security,” says Srai.
“Technology, supply chains and the way markets and regions develop become interesting change agents. I believe that our research network will be able to anticipate these changes,” he adds. “It’s only by understanding a company’s overall global supply network – a ‘whole system’ approach – that it’s possible to appreciate the opportunities and the benefits that can emerge for doing things better, wherever you are in the world.”
This article originally appeared on the University of Cambridge website.
Image - Increasing the efficiency of food supply chains can decrease wastage
Credit: Neil Palmer (CIAT)
You also might be interested in:
![]() |
Working with multinational companies to capture value from their international operations |
Find us on
Date published
8 October 2015