Additive manufacturing: understanding the bigger picture
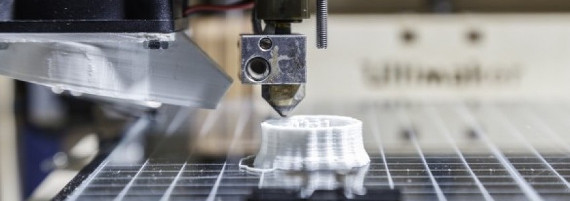
Governments around the world have high hopes for Additive Manufacturing (AM) – also widely referred to as ‘3D printing’. But if it is to have the economic impact they are looking for, there needs to be a better understanding of both the huge opportunities AM presents as well as the barriers that may prevent it realising its potential.
The IfM is undertaking a multidisciplinary research project, jointly funded by the EPSRC and the ESRC, to understand how AM will affect the manufacturing landscape and how UK firms can become global leaders in it. The research team is also supporting the development of the UK’s National Strategy for Additive Manufacturing.
AM technology and its potential is still characterised by uncertainty. While there is an ever increasing interest in AM, our research indicates that there is still a lack of awareness of what it can do and how it can translate into economically viable business models. Spare parts are an interesting example. They have been highlighted by some as an area in which AM could have a major impact on current manufacturing activities. However, when analysed from a business and technology perspective the model quickly breaks down. While it makes perfect sense for the International Space Station – or a nuclear submarine - to be able to ‘print’ its spares in situ the model becomes less clear as you extend into less specialist environments. For example, repairing failures in container ships in the middle of the ocean might also seem to be an opportunity to apply this technology. However, once all the constraints of what can actually be printed on-board have been taken into account, it may prove more practical to get spares or do repairs via more traditional means. Extend the model even closer to home and it breaks down completely. If a local car dealership were to print its own spares, for example, the parent company would incur significant costs to train a franchisee and the risk of failure – and subsequent brand damage for the parent company – could be just too great.
As well as this lack of clarity around viability, we see a range of other barriers relating to the technology itself. While, in many respects extremely advanced, AM is still dependent on a surprising amount of ‘craft’ or low tech, manual interventions. And this has a number of implications for scaling up. With other manufacturing processes we have had hundreds of years to understand them and get them right. But we do not have complete data on these new processes, either because it does not exist or because individual companies have no reason to share it in this highly competitive environment.
What are we likely to see over the next few years? The hype around consumer applications will start to recede as we realise that we are not all going to have 3D printers in our own homes in the near future. But industrial applications will steadily advance and consolidate in areas such as life sciences and aerospace. We are also likely to see interesting international developments, such China using AM to help shift its manufacturing from high-volume to high-value add, Germany leading on the integration of AM into the broader ‘Industrie 4.0’ transformation, and many countries including the US and Singapore seeking to link AM adoption and entrepreneurship to create new opportunities for value capture.
This article first appeared in UK Manufacturing Review 2015 – 2016 published by Stirling Media Ltd.