Why the skills gap is a major barrier to the adoption of additive manufacturing
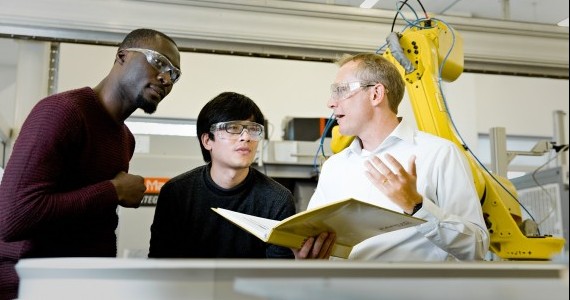
This article first appeared in the July/August issue of The Manufacturer magazine.
Additive manufacturing has enormous potential, which – if fully realised – will transform product development and supply chains in the UK. It offers the prospect of on-demand, mass personalisation, with more localised, flexible and sustainable production.
As a result, additive manufacturing is being heralded as a technology that is forecast to be worth £67bn globally by 2020. It has been predicted that the UK could win a £5.7bn share of the additive manufacturing market and produce 63,000 new jobs by 2020.
Skills for now and the future
To enable the UK to maximise the opportunities and benefits of additive manufacturing, we need to identify and address the barriers to its wider adoption. The most-common barrier identified by industry is a lack of appropriate skills in design, production, materials and testing. This includes both a need to up-skill the current workforce and train the next generation.
In addition to the sheer numbers of people that need training, another major challenge is a consequence of additive manufacturing not being a single technology. Additive manufacturing involves a multitude of technologies, each at different levels of technological maturity.
It also has different subdomains of knowledge that need to be considered, such as process technologies, materials and software. There is a need to identify, document and agree on standards for the core knowledge relating to additive manufacturing.
But, given the wide diversity that falls under the banner of additive manufacturing, it is difficult to agree on what knowledge and standards to include in a ‘core curriculum’ for training people in additive manufacturing.
We have centuries of knowledge about manufacturing through casting, forming and subtractive processes for a wide range of materials, and the bulk of this knowledge is in the public domain. But additive manufacturing, while rapidly developing, is still in its relative infancy, and significant amounts of knowledge rest within companies who, for quite understandable commercial reasons, may not want to make this freely accessible. There is also the issue of who will define and own the standards, and who will make sure that they are updated as the technologies evolve.
The nature of training
When and how should additive manufacturing skills be learned? There needs to be consideration of the positioning of additive manufacturing skills development for those in full-time education, as well as those already in the workforce.

Additive manufacturing skill development needs to be structured for learning at school, college, university and through continuing professional development. Additive manufacturing is a great opportunity to introduce primary pupils and their teachers to what modern manufacturing – in all its exciting and diverse forms – is really about.
It will also help address the sometimes inaccurate and incomplete perceptions of ‘manufacturing ’ held by many primary school children and their teachers.
There is also the broader potential for the adoption of additive manufacturing in addressing the widely publicised problem of the impending shortfall of engineers entering the UK workforce.
Additive manufacturing is providing a route by which the younger ‘digital natives’ can connect their virtual skills with the production of real artefacts, and hence re-establish a link to manufacturing.
It is also interesting to consider the flipside of the issue, i.e. how might education be changed as a result of additive manufacturing adoption? Examples of this can already been seen in the use of additive manufacturing in the training of surgeons, through the printing of 3D models of organs scanned from patients to improve surgical outcomes, and the adoption of 3D printers in engineering, science and design departments in universities for rapid testing, and production of low-cost lab equipment.
So, there are two key messages to take away. First, we need to define the what, when and how of skills development for additive manufacturing – and that is going to be a complex and ever-changing task. Second, we mustn’t lose sight of the fact that additive manufacturing adoption has the potential to kick-start the transformation of many other aspects of our economy. Thankfully, much of the hype-driven nonsense around 3D printing of the past few years is lessening, and we now have the opportunity to focus on capturing the real potential of these transformative technologies.
If these barriers can be addressed, additive manufacturing has the potential for substantial value creation and capture in the UK. A failure to do so risks UK manufacturing falling behind in the new world of Industry 4.0.
Researching the potential of digital fabrication for the UK economy
Dr Minshall led a joint ESRC and EPSRC-funded national research project to examine the reality and the potential of digital fabrication for the UK economy. The project delivered three key outcomes:
- Determining the effects of digital fabrication on the organisation of manufacturing in the UK
- Assessing how and where value will or could be captured in the UK
- Identifying key support actions necessary by UK policymakers to underpin value capture resulting from digital fabrication in the UK.
Read more at: www.dfab.info or contact tim.minshall@eng.cam.ac.uk