Photofabrication: photochemical specialist firm achieves sustainable energy savings
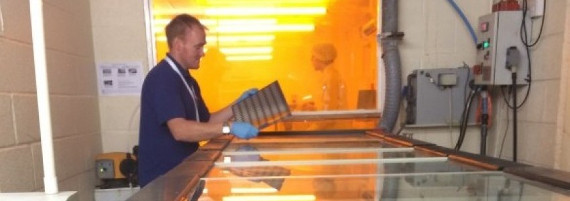
Photofabrication is just one of around 100 smaller manufacturers that IfM ECS is working with as part of the PrISMS programme – and this case study highlights the difference it has made. Photofabrication is a specialist photochemical machining company that produces metal products including filters, gaskets and laminations for the aerospace, defence, life sciences and other sectors.
IfM ECS worked with Photofabrication as part of the PrISMS programme to:
![]() |
reduce energy use to save £30,000 a year |
![]() |
reduce the environmental impact of core processes |
![]() |
cut power consumption per etched sheet by 33% |
![]() |
ensure the firm has resources to tackle business constraints |
![]() |
establish strategic priorities for the medium term |
![]() |
improve managers’ effectiveness and increase delegation |
![]() |
identify and help recruit a technical director. |
Photofabrication is a specialist photochemical machining company that employs around 50 people and produces intricately shaped metal components. Services include chemical etching, plating, laser cutting and metal stamping for products such as filters, gaskets, springs, laminations and spacers. Its operations range from prototype to production in most sectors requiring metal components – aerospace, automotive, communications, defence, life sciences, medical and security.
Founded more than 40 years ago and based in St Neots, Cambridgeshire, it is a leader in developing technology to produce intricately shaped components – it has produced more than 60,000 different components so far. The firm says: “If you can draw it, we can make it – as long as it’s in thin sheet metal.”
Annual turnover is around £3 million and the company has between 6,000 and 8,000 orders a year. It focuses on high-value, low-volume orders (sometimes for as few as a handful of metal sheets) and strives to offer the best service and highest quality components within the shortest possible lead times.
Most of its customers are in the UK – in its increasingly sustainable business model, it can minimise transport costs and keep closer control of its supply chain. It aims to offer a three-day turnaround at a premium to customers in the UK, the north of France and Germany.
Working with IfM ECS
IfM ECS worked closely with the company to establish a clear understanding at team leader level of the priorities for the business. A key step was the IfM ECS Prioritisation process, a whole-business diagnostic and action planning tool, which helped the firm to understand its strengths and weaknesses and draw up an action plan to address them. This has led to team leaders establishing a process to allow them to manage their areas more effectively and to enable the operations director to delegate more effectively to them.
IfM ECS helped to identify and recruit a technical director to make the management team more effective in the medium term. There was continued engagement with the operations director to ensure the company has the resources to tackle those issues likely to act as a constraint on the business. The company has invested in staff training and the role of middle management has been developed to improve the day-to-day running of operations. Supervisors also take more responsibility and monthly reviews of processes have been replaced by weekly, daily and hourly checks.
New lines were introduced in the factory to increase capacity and the firm is constantly working to reduce lead times. The firm has set standards for delivery, quality and health and safety and runs regular projects across its seven departments to further raise those standards.
It was recognised that the company would benefit from specialist advice to help improve both its energy usage and environmental impact. This advice was provided by Ecopare, a project partner of IfM ECS in PrISMS.
Energy audit and benefits
One of Photofabrication’s core processes is etching metals using concentrated acids. This process has by-products which could pollute watercourses and are both costly and difficult to dispose of responsibly. The company benefitted from specialist help provided by Ecopare under the PrISMS programme. Ecopare provided detailed recommendations about how to improve both its energy usage and its environmental impact.
Changes made as a result of the assessment included:
![]() |
eliminating the need to heat the etching tanks |
![]() |
reducing lighting bills by about 60% through the introduction of LEDs |
![]() |
purchasing a new compressor resulting in recurring energy savings of £8,000 per annum (the capital cost was recovered in eight months) |
![]() |
as a result of these actions, the power consumption per sheet etched fell from 12.5 kWh to 8.4 kWh within 12 months – an improvement of 33% |
![]() |
water usage has become more efficient, including using recycled water |
![]() |
a large investment in effluent treatment means a reduction in metals (nickel, copper, chromium and zinc) in the discharge from 7 parts per million to just trace elements |
![]() |
implementation of a formalised energy management policy by adopting ISO14001 |
![]() |
these changes will produce energy savings of £30,000 per year – and all of these improvements can be sustained or enhanced. |
Paul Rea, operations director, says: “We felt we knew our energy use well but they came at it from a different angle. That allowed us to look at things we would not have looked at. We were using an amazing amount of electricity over the weekends. We have reduced this quite considerably.”
Additional energy savings could be realised with continuous electrical consumption monitoring via a dashboard/portal that would allow for a programme of continuous optimisation of energy.
Further energy savings could potentially be achieved by reusing waste heat from existing processes or adding a combined heat and power system which could produce ‘free heat’ to further reduce the electricity bill by up to 30%.
Assessing the impact of IfM ECS’s engagement with the company, Paul says: “We have worked closely with IfM ECS and we see the benefits. It allows us to tap into resources we don’t have, to see things in a different way and to make decisions on that basis.
“Systems and processes have been put in place, such as continuous improvement, that allow us to go from strength to strength. We have a different mindset – it’s about getting better all the time.”
For more information on Photofabrication visit here.
PrISMS The PrISMS (Practical & innovative Solutions for Manufacturing Sustainability) programme aims to transform the growth prospects of 50 start-ups and 70 smaller manufacturers across the Eastern Region – creating more than 140 new jobs and safeguarding many more. The programme is funded by the European Regional Development Fund (ERDF), with match funding from the EPSRC Centre for Innovative Manufacturing in Industrial Sustainability, ideaSpace and IfM Education and Consultancy Services (IfM ECS) and supported by 11 county and district councils in the region. It is managed and delivered by IfM ECS, which bases its methods on research at the University of Cambridge’s Institute for Manufacturing (IfM). For more information visit here. |
IfM ECS IfM Education and Consultancy Services works with companies of all sizes to help create and capture value and with national and regional governments to support and grow their industrial sectors. It does this by transferring the new ideas and approaches developed by researchers at the Institute for Manufacturing (IfM) through a programme of education and consultancy services. IfM ECS is owned by the University of Cambridge. Its profits are gifted to the University to fund future research activities. For more details on its work with SMEs visit here. |
ERDF PrISMS is part-financed by the East of England European Regional Development Fund (ERDF) Programme 2007-2013. The Department for Communities and Local Government is the managing authority for ERDF in England, which is one of the funds established by the European Commission to help local areas stimulate their local development by investing in projects which will support local businesses and create jobs. The East of England ERDF programme (covering Bedfordshire, Cambridgeshire, Essex, Hertfordshire, Norfolk and Suffolk) supports low carbon economic growth and has allocated approximately €95 million. |
Download the case study here.
For further information about the work of IfM ECS in the PrISMS programme please contact contact Nicky Athanassopoulou on +44 (0)1223 760376 or naa14@cam.ac.uk; or John McManus on +44 (0) 1223 764908 or jm694@cam.ac.uk.