Three Dimensional Laser Surface Modification
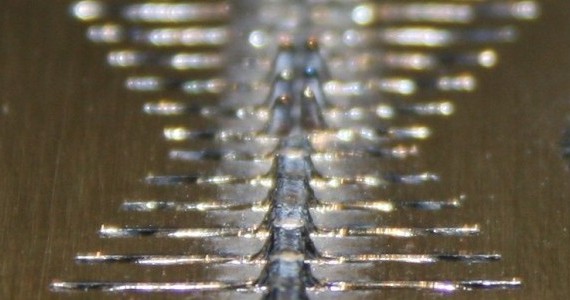
3D Laser surface modification enables features to be formed from the substrate material. The process is based on the Surfi-Sculpt® manufacturing technique originally developed by TWI Ltd. using electron beams with electromagnetic coils to deflect the beam. Using a laser beam as the power source offers advantages such as generating these novel surface features in atmospheric conditions. The technique enables surface features to be produced on a range of substrates including metals, polymers and ceramics.
Aims
- Establish optimum processing parameters for a range of both materials and processing environments.
- Gain a greater understanding of the Surfi-Sculpt® process in terms of the physics involved. Initially comparing to phenomena such as weld humping.
- Develop techniques and methodologies to address rapidly growing markets for surfacing and machining.
The process
The Surfi-sculpt process is characterised by repeated laser swipes making multiple returns over the same area inducing material movement to sequentially build surface features. It is thought that this is due to a combination of surface tension effects in the melt pool due to temperature gradients and heat management between repeated swipes.
- Intense laser beam power to melt material
- Laser beam translation
- Hundreds of repeated translations
- Feature formation
![]() |
Figure 1 - Schematic of feature formation process |
Fiber laser and scanning system
The Laser system consists of a 1064nm fiber laser between 200W and 1kW attached to a scanning system. Two galvanometer driven mirrors are use to scan the beam whilst a post objective lens focuses the beam as shown in figure 2. This system enables focusing in three dimensions.
|
Figure 2 - Functional principle of post-objective scanner (photo by ARGES) |
Features
A wide range of features can be produced ranging from single run lengths producing thin features to star features as showing in figure 3, All swipe formations require multiple repeats and the heat management between them.
![]() |
Figure 3 - Star Feature |
- Creates protrusions up to 3.8 mm in height, to date.
- Corresponding intrusion is also produced.
- Rapid manufacturing at potentially 0.53 seconds per feature if small, presuming that multiple features are being produced during the delay intervals. Array size can be used to achieve larger delay times without compromising on processing times.
It may also be possible to produce features upon existing features by applying multi-stage treatments that have already been successfully employed by electron-beam surfi-sculpt®. This was achieved by producing a star feature and then rotating it 90° and repeating the process. Multiple additional features can potentially be produced from the original feature.
![]() |
Figure 4 - Multi-stage treatment by repeating process with original feature rotated 90° |
Physical Theory
The Surfi-sculpt process occurs within similar parameter ranges to that of the humping phenomenon in welding and it is thought that the processes are related. Surfi-sculpt also occurs at speeds slightly lower than humping and therefore pre-humping mechanisms are also considered.
High speed imaging has revealed that oscillations occur in the melt pool following the laser material interaction. It is suggested that these oscillations are due to a Kelvin–Helmholtz instability of the surface melt layer. The strong material and shielding gas influence seen to date in production of Surfi-Sculpt also suggests influences of surface tension and Marangoni convection.
Acknowledgement
This work is funded by the EPSRC and TWI Ltd. The authors would like to thank the Engineering and Physical Sciences (EPSRC) Engineering Instrument Loan Pool and Adrian Walker for the high speed camera and Cavilux HF laser. Dmitry Badyukov, from Arges GmbH, for his help with programming the scanner. Ali Khan, from TWI, for his helpful suggestions of experimental methods and stimulating discussions.
Applications
- Heat exchanger and heat sink surfaces
- Composite to metal bonding
- Ultra-thick coating deposition
- Orthopaedic implants
- Aerodynamically and hydro-dynamically enhanced surfaces
Publications
Earl, C., Hilton, P., Blackburn, J. and O'Neill, W: A Comparitive Study of 3D Laser Surface Modification and the Humping Phenomenon, 30th International Congress on Applications of Lasers and Electro-Optics (ICALEO) 23 - 27 October 2011, Orlando, FL. USA.