Worker assistance systems: Understanding the human perspective
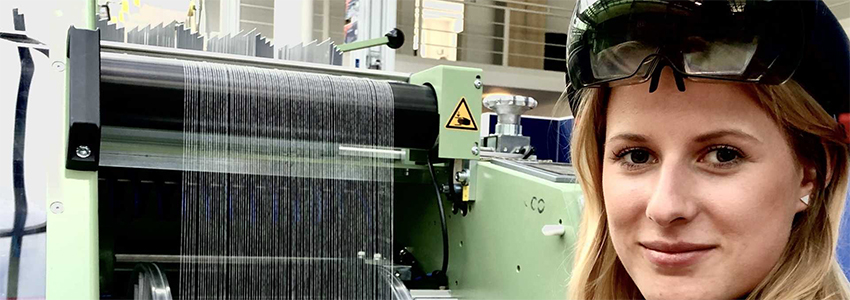
26 June 2020
By Mirco Möncks, Elisa Roth and Thomas Bohné
The future of manufacturing is often characterised by an increase in complexity, efficiency and sustainability. As the execution frequency of simple and repetitive tasks decreases, manual tasks are likely to become more complex.
Does this mean that manufacturing is inevitably heading towards full automation? It depends on who you ask.
According to our recent study, the expected degree of automation on future shop floors seems to depend on one’s position in the hierarchy of an organisation – but different to what most would intuitively expect.
Human-Machine Interaction: Worker assistance systems on future shop floors. Image: Marie Roth
We asked three groups – manufacturing executives, instructors and operators – about their perspectives on worker assistance systems to uncover their experiences, what kind of assistance systems they would find acceptable, and to what extent their experiences and views of the future aligned.
Worker assistance systems are physical or cognitive support systems for human operators; for example, an exoskeleton which supports operators by enhancing their physical strength, or an augmented reality system that offers cognitive support, like digital instructions during an assembly process.
We found that operators expect a technology-centric scenario and fear that they will not be required due to ongoing automation. Executives and instructors, on the other hand, believe lights-out factories or total automation are unlikely to become the new normal.
In fact, the rising complexity of production may require manufacturing skills which cannot be efficiently automated. Executives anticipate an integrative scenario, in which both robots and operators will work together on the shop floor.
This difference in perspectives is a potential barrier to users’ acceptance of and adaption to such products. Manufacturers considering or deploying worker assistance systems without understanding users’ perspectives risk poor results. Therefore, it’s essential they understand these diverging perspectives better and how to tackle them.
Suitability of worker assistance systems
Worker assistance systems are expected to be mainly complementary, cognitive support systems for operators performing tasks related to diagnosis and optimisation, or standard operating procedures – like the example of the operator with digital assembly instructions.
While the work of human operators in manufacturing is continuing to shift, human operators are likely to remain in control of operations on the shop floor for the foreseeable future.
Major applications of assistive technology are expected in: variety and exception handling; support of complex standard operating procedures; data analysis, diagnosis and optimisation, and digital engineering.
The exception is anticipated to be in work areas such as the manufacturing of components and inbound logistics, where the number of manual tasks is likely to decrease and, eventually, human operators may become redundant.
Acceptance of assistive technology
In general, executives and instructors take a human-centric, integrative perspective on future manufacturing. That is, given the acceptance of operators, the fulfilment of relevant safety requirements, and economic effectiveness, executives and instructors welcome assistive technology on shop floors.
In industrial learning scenarios (e.g. an apprenticeship), operators also welcome extensive cognitive support to quickly acquire complex skills and learn at their individual pace. In fact, many operators would potentially accept a ‘robot teacher’ supervising their progress and providing individual real-time feedback.
After finishing their practical training programmes, however, operators’ attitude towards worker support systems seems to change. Experienced operators seem to reject assistive technology that aims to give explicit training or technological support during tasks which they perceive themselves to have a degree of mastery.
Operators also strongly prefer a support initiation mechanism that is controlled by them rather than an autonomous initiation mechanism triggered by sensors and intelligent systems.
When compared with the acceptance of cognitive support, operators’ opinions on body-worn technology for physical assistance (like exoskeletons) appear more reserved.
Operators are excited about the potential of physical assistance systems, but they fear negative effects on both their physical and mental health.
Likewise, executives and instructors expressed general concerns regarding the implications on the long-term health and safety of operators. For example, when being guided by digital instructions on an augmented reality headset throughout the entire working day, operators’ natural cognitive abilities could potentially be affected.
Executives especially pointed out that they aren’t aware of any medical studies examining the long-term implications of worker assistance systems on the operator’s mental and physical health.
Experiment: Teaching Worker assistance systems how to recognise operators’ activities. Image: Elisa Roth
Human-robot collaboration or co-existence?
Close human-robot collaboration is a much-touted operating model in future manufacturing. However, most stakeholders across the hierarchy of organisations in our study don’t believe it is currently feasible – that it is more hype than reality.
We identified three underlying reasons for this perspective:
- strict regulations for occupational health and safety,
- an insufficient amount of potentially beneficial use cases,
- restrictions by product and process properties. In fact, as part of our study we could not identify a manufacturing organisation that has effectively implemented collaborative robots within their serial production.
Human-robot co-existence, on the other hand, seems feasible to both executives and instructors. In other words, humans and robots working towards the same goals, but in timely or physical distance.
In this scenario there is no intent to replace the human operator on the shop floor. Instead, the operator stays in full operative control and responsibility. Worker assistance systems are deployed as tools which are assisting or supporting the decision-making process of the operator.
Robots, on the other hand, are deployed to perform jobs which could cause potential harm to humans or where partial automation is considered more effective for the overall operator’s productivity.
Regardless of the operating model, the perceived importance of human operators on future shop floors seems to correlate with the informants’ position in the organisational hierarchy. Executives expect human operators to remain an essential necessity on future shop floors. Instructors and operators, on the other hand, expect a future characterised by automation.
Recommendations
When thinking about assistive technology it is paramount to carefully consider the individual circumstances of manufacturers and their stakeholders in industry.
Assistive technology will change the way humans work on the shop floor, how they interact and collaborate with machines. Assistive technology, however, is not about designing the most advanced technology.
It is also not about engineering prototypes which never make it to a single shop floor. It is about meaningfully assisting humans and their skills.
Assistive technology will not be the silver bullet that solves all the most pressing challenges in a manufacturing organisation. However, some assistive technology, especially cognitive assistance systems, is becoming increasingly feasible to deploy while maintaining a human-centric perspective.
Manufacturing organisations should therefore be more actively communicating the value and necessity of operators on their future shop floor.
Six recommendations to manage assistive technology
- Involve all stakeholders throughout the hierarchy of your manufacturing organisation. Their perspective may differ, but only if assistive technology is accepted can it be successful.
- Communicate the joint value of assistive technology and human skills to your staff. Operators might fear that assistive technology could be the last step before being made redundant.
- Develop your staff. To cope with rising complexity and use, assistive technology operators will need a more sophisticated skills portfolio.
- Choose the right applications. Variety and exception handling, support of complex standard operating procedures, and digital instructions for standard operating procedures might by beneficial starting points.
- Focus on cognitive abilities and support systems. Operators tend to reject assistive technology enhancing their physical strengths.
- Co-existence often may be all you need. Collaborative robots currently do not seem feasible on most shop floors.
This article was originally published in The Manufacturer.