Boosting industrial sustainability through transformative technologies
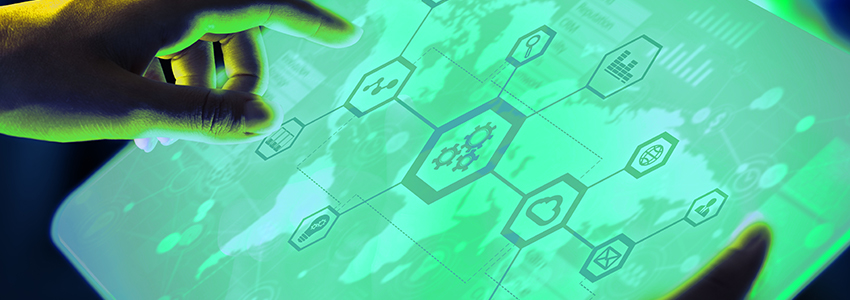
How might digital technologies contribute to a more sustainable industrial future?
The smartest manufacturers are already working towards strategies which can both improve their sustainability practices and simultaneously deliver on business objectives. Among these leaders, there is innovative thinking about the role for digital technologies can play. But what might this look like? Professor Steve Evans, Head of the Centre for Industrial Sustainability, shares his insights.
According to the World Economic Forum, the term ‘sustainable development’ can be defined as development that increases the living standards of current generations without sacrificing that of future generations. Manufacturing is a major contributor to modern well-being, but at the same time a contributor to many of the industrial and environmental challenges we recognise today.
So what potential is there for manufacturing to become more sustainable without negative business consequences? More positively, what prospects are there for creating sustainable practices which actually improve profitability and growth?
Forward-thinking industrialists and policymakers are beginning to explore the role that emerging technologies can play in the move towards improved sustainability and resource efficiency. Digitalisation in manufacturing and across supply chains can deliver many innovative capabilities into the industrial system, through increased data, greater connectivity, more flexible automation, and increased analytical capability. Most importantly, it is the convergence of different technologies used in combination that is predicted to change manufacturing systems substantially over coming years.
Three phases of sustainability development through digital technology
Through our research in the Centre for Industrial Sustainability at the Institute for Manufacturing, we have identified three phases of major change that can be achieved through digitalisation in contributing to a sustainable industrial future.
Digital technologies offer specific opportunities that can support a pathway to a sustainable industrial system, as illustrated in Figure 1. First is the ‘resource productivity’ phase, in which industrial digital technologies will be used – and are already being used – to help factories do more with less. Second is the ‘resilience’ phase, in which digital technologies will be used to help industry become more resilient to the many disruptions we can expect. Finally is the ‘sustainability’ phase, in which emerging technologies will be used to help the industrial system live within its means.
Figure 1: Three phases of sustainability development through digital technology
Source: © Evans, S.E., University of Cambridge
Let’s consider each of these phases, with some examples of how transformative technologies for improved industrial sustainability can be applied in practice.
Phase 1: Resource productivity
Making more efficient use of resources is increasingly an area of focus for leading manufacturers. These firms understand that resource efficiency makes sense both from an environmental sustainability perspective, and in cold, hard financial terms: better use of resources (energy, materials, water and waste) goes hand-in-hand with improved cost control and increased profitability, as well as encouraging more innovative ways to grow productivity and create value. And they are developing capabilities to achieve this, including through transformative use of digital technologies.
Industrial digital technologies can enable a radical improvement in the use of non-labour resources, on a scale not yet achieved. While many economies have achieved growth in labour productivity, often the highest and most intransigent costs lie in non-labour resources. In the UK, for example, labour makes up only 10% of a typical manufacturers costs, while 50% of costs are in materials, parts, energy and utility costs, which have been stubborn to yield similar productivity gains to labour.
Benchmarking analytics is one way in which digital technologies can improve resource productivity. This can be done through analysis of the vast quantities of data generated within a factory, to identify certain times of the day or week when production is less intensive in its use of resources. These ‘golden moments’ indicate times when we can manufacture one product with, for example, half the energy or CO2 emissions of the same product manufactured at a different time. Similarly, data analytics can be used for anonymous comparison between factories to identify resource consumption patterns and help establish windows of opportunity when more resource-efficient production is possible. A UK study has estimated that such practices could yield up to £10 billion extra profit for the UK manufacturing sector by lowering material, energy and utility costs, while simultaneously delivering 4.5% CO2 reduction for the UK.
However, unravelling large and complex sets of data to make sensible comparisons is technically challenging. Pioneering technology providers are beginning to emerge in this space. IntelliSense.io is one such example: a market leader in industrial Internet of Things (IoT), machine learning and artificial intelligence. Their platform can help to eliminate inefficiencies and improve productivity yields in plants, processes and people, through analysis of real-time and historical data to predict and simulate future performance. These enable IntelliSense.io users to monitor the quality and safety status of materials during transportation, track the supply chain end-to-end and identify and respond to any bottlenecks more quickly, along with other capabilities. Reduced performance variability, less unplanned downtime, and optimised use of resources lead consequently to lower energy consumption and associated costs.
Augmented reality is another valuable technology to this drive for resource productivity, as it enables engineers to see energy, water and waste flows in real-time in the factory setting. Firms can use AR to apply the traditional skills of productivity improvement enhanced with deep layers of data to pinpoint areas for operational improvement. We can expect such AR technology eventually to lead to improved factory design tools.
The scale of benefits from using digital technologies to make previously hidden or messy situations visible represents a significant reduction in total costs for manufacturing firms, as well as benefits to the energy grid and to climate targets.
Phase 2: Resilience
How should manufacturing firms be developing more resilience in the face of a variety of potential disruptions? Risks include disruption from floods, droughts, interruption of energy supply and of the availability of materials, and governments are predicting that many of these risks are currently increasing due to a combination of climate change and geopolitics.
A primary strategy to mitigate such disruptions is to reduce the resources required per unit of value add. The drive towards improved resource productivity, as in Phase 1 above, will help to achieve this.
But the industrial system is part of wider energy-food-water-waste systems, and can offer significant performance improvements into those systems, as well as to itself.
Energy resilience is a key area of focus. An example of a company leading the way is OpenEnergi, a growing technology company that deploys sensors to identify short term strain on the energy grid and uses IoT technology to adjust for electricity being consumed by industrial equipment for short bursts. Units such as refrigerators or heating systems can be briefly adjusted in their energy usage to respond to short peaks in electricity consumption elsewhere, and thereby perform a service to the grid in helping to balance electricity supply and demand. This ‘demand side response’ service is a type of demand flexibility, and part of a wider shift to a smart energy system. The next stage for extending these capabilities is through connecting factories or supply chains, or even local clusters of factories, to energy grids in a way that delivers grid services such as demand shifting peak-lopping and frequency response (what we refer to as factory-to-grid (F2G)).
Material efficiency is another area of fertile ground for improving resilience through digital technology, through reuse of waste. There is exciting potential for many factories to use waste from other factories as an input material. However, typically the provenance, quality, and time availability of such materials preclude their inclusion into a carefully planned system where the factory does not want to stop production while waiting for raw material to arrive. Digital technologies can now be deployed to predict future waste availability and quality to an accuracy never before possible. There is a likelihood of new solutions providers emerging, offering manufacturers services to increase waste exchange.
Benefits of improved resilience across national economies include reduced downtime for factories, increased export orders due to predictable delivery, and good environmental performance. Initiatives such as demand side response can help to decrease energy costs, reduce or even eliminate energy disruption, and lower carbon emissions (through reduced reliance on fossil fuelled power stations for balancing energy grids).
Phase 3: Long-term sustainability
Ultimately, global manufacturing must transform for long-term sustainability, operating within the planet’s ability to provide raw materials, energy and water.
It is evident from our cross-sector studies that many manufacturers, both large companies and SMEs, are engaging with this ambition with increasing seriousness.
One such example is Unilever, which hit its target to send zero hazardous waste to landfill across over 230 factories 3 years early. While AB Sugar’s innovative transformation of its Wissington refinery over a 10 year period, moving to zero waste through maximum valorisation of all its material flows, has set a high standard for others to follow. However, it is also evident that such motivation is still far from widespread.
Long-term sustainability can represent a paradigm shift in the conceptualisation of how manufacturing works. Take the idea of a foraging factory. This uses similar technologies to the waste exchange factories described in Phase 2, to identify what raw materials are likely to become available locally and when. Extending this approach, a foraging factory would then search its order book to assess what products can be made with those locally available materials, and calculate how to adjust the bill-of-materials for that product to allow it to be made from waste that is becoming available. This is only possible because of the extreme flexibility emerging from digital automation and process control technologies.
Ecover have been experimenting with such a factory in Mallorca (see box), and other pioneering factories are conducting similar experiments out of the public eye.
The ‘Friday night fridge problem’ on an industrial scale
Mallorca is a Spanish island in the Mediterranean, which attracts around 16 million tourists each year. Although the Mallorcan economy is heavily dependent on tourism, the small island is experiencing damaging environmental impacts as a result. Hotels, for example, generate a high demand for washing detergents and cleaning products, which can have detrimental effects on the local ecosystem, harming the island’s natural beauty which attracts the tourists in the first place. These cleaning products are expensive to bring to the island by boat, and create emissions in the process.
So is there a better way? A pilot project with Ecover (a company which makes ecologically sound cleaning products) and Forum for the Future (a not-for-profit organisation working on sustainability initiatives), explored using waste streams from existing agricultural production on the island for local production of environmentally sustainable cleaning products. Working with landscape intelligence company Rezatec the project was able to use satellite data analytics to map the agricultural waste streams becoming available on the island at any given time.
Using precision farming techniques, the satellite data can predict when crops (including the citrus fruits, olives, almonds, almond flowers, grapes and carob trees grown on Mallorca) will be ready to harvest, and allow factories to plan when waste streams such as stalks and leaves will become available. A searchable database then allows scientists to identify the appropriate product varieties that can be made using the available ingredients (such as lemon-scented detergent) and create the appropriate enzymes needed from computer-designs. Cans containing the products are reused and refilled with new products.
This brilliant combination of advanced technology with local, small scale production is a bit like the ‘Friday night fridge problem’ – you look in the fridge and are low on food, but need to work out what you can cook up with what’s left. Sometimes the most creative recipes start this way!
The aspiration is to have an island economy which balances and integrates three key economic activities – tourism, agriculture and manufacturing – which will move to supporting each other, creating jobs and adopting a fundamentally sustainable local model of production and environmental protection.
Figure 2: Ecover’s vision of an industrial system on Mallorca
Source: Murthy, Sudhir R., "Designing Sustainable Industrial Systems: Principles–Patterns–Practices", PhD diss., University of Cambridge, 2016
This kind of approach creates a fascinating juxtaposition of superbly advanced technologies such as big data, satellite-driven precision farming and computer-designed enzymes, with the philosophies of traditional cottage industry. It’s about using whatever natural resources are around you, when they become available, by harnessing digital technologies to achieve this. The results are ground-breaking: enabling more sustainable manufacturing at a lower cost, creating new jobs and local economic benefit in the process. It’s where the big data, super intelligent world meets old-fashioned principles of thrift and valuing resources, and is likely to be fundamental to future thinking in manufacturing if we are to achieve long-term industrial sustainability.
This article is written by Professor Steve Evans and was originally produced for the Manufacturing Leadership Council.
You may also be interested in
Centre for Industrial Sustainability - The Centre for Industrial Sustainability (CIS) works to develop knowledge and tools that accelerate the transition towards a sustainable industrial system.
IfM Sustainability Association – The Sustainability Association is a membership network of manufacturing leaders and world-leading researchers looking to drive sustainable change to new levels in manufacturing organisations.
Reducing waste in manufacturing - view an article that explores how to reduce waste, showing that it is possible to also generate additional value in doing so.