Scalable customisation
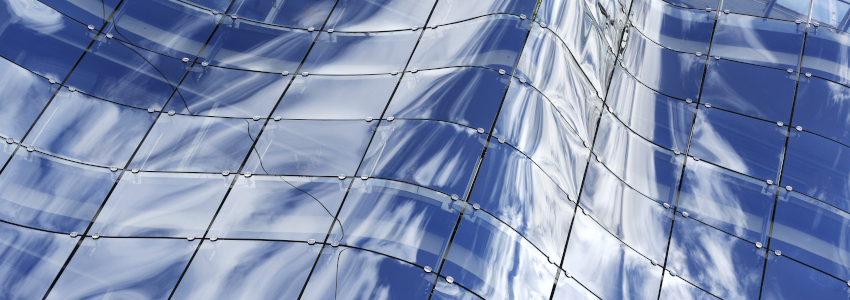
How can manufacturers develop sophisticated customisable products at scale, which are affordable both for the manufacturer and for the consumer? Customisation is no longer the exclusive domain of the wealthiest: the demand from mass markets, both business and consumer, is for increased ability to personalise products. Manufacturers are seeking ways to deliver this customisation in higher volumes at lower unit cost.
Dr Ronan Daly and Dr Cristina Rodriguez-Rivero from the Institute for Manufacturing, University of Cambridge, provide an insight into an example of late-stage customisation, through their research group’s collaborative project with multinational glass manufacturer NSG Pilkington.
Innovative manufacturers are pursuing approaches for making customisation more affordable, responding to market opportunities to address increasing consumer demand for personalised products. The prize is to gain competitive advantage and customer loyalty by delivering customers with the specifications of their choice whilst keeping the costs of production low.
Moves towards “mass customisation” can be supported by emerging technologies which enable product features to be added to order at a late stage in the manufacturing process.
New applications of advanced inkjet printing technology provide one such example. Our Fluids in Advanced Manufacturing research group at the Institute for Manufacturing has been working with glass manufacturer NSG Pilkington, exploring technologies for printing customised embedded electronics, sensors and other features into curved glass surfaces at scale. This is a technically challenging process, but offers tantalising potential: rather than embedding the electronics into the glass earlier in production, the use of inkjet printing technology allows late-stage customisation to order. We are investigating how the capabilities offered by inkjet can be scaled up for customisation that is affordable both for the manufacturer and the customer.
Customising curved glass
Large curved glass products are used in many different types of product. In certain applications, such as automotive glass products – mainly windscreen, windows and mirrors – production involves a range of multiple-layer processing steps before the glass is formed into curved shapes. The current manufacturing of float glass and advanced coatings is only efficient with continuous production, but can make customisation difficult and costly if it happens early in the production process.
NSG Pilkington’s R&D team has identified that inkjet printing can enable customisation at a later stage in the process. A range of product features (including embedded sensors and security features) can be added using inkjet, through advanced functional material deposition directly to product surfaces.
A particular challenge is to identify new techniques for printing directly onto larger curved surfaces. Existing technologies for achieving this have limitations: these include continuous inkjet printing (CIJ) which is used for printing barcodes and best before dates to items like small bottles, but this can be limited in terms of achievable colour and precision over larger surfaces. Drop-on-demand printing has recently seen a renewed interest in printing to complex shapes but will face severe challenges in terms of precision and predictable drop placement when working on non-flat surfaces.
With this process, airflows can have a significant impact on accuracy, causing misplacement of ink droplets. Our research team at the Institute for Manufacturing has been working to characterise the influence of surface texture and curvature over aerodynamics of inkjet printing.
One of the other technical issues with printing on to large or complex surfaces is that the printhead itself needs to be moved across the product. This is different from the existing solutions where the product is the moving element, using automation to enable simple, smaller curved surfaces to move past the inkjet printhead.
To develop an improved understanding of printing direct-to-shape, we are working with NSG Pilkington to map the detailed surface textures and chemistries that will need to be coated. We can then examine with ultra-high speed imaging the surface impact and drying dynamics of advanced functional material inks.
Understanding airflows
There is a strong link between misplacement of ink droplets and the surrounding airflows. We are working to understand this better, in order to improve the ability to deliver sensors, responsive surfaces and electrical pathways to non-flat surfaces. To do this, we apply advanced visualisation techniques to study droplets and airflows in commercial and in-house equipment to analyse the effect of a variety of printing parameters.
Dr Cristina Rodriguez Rivero joined IfM in 2014 as a Research Associate and is focused on droplet and jet behaviour, inkjet visualization techniques, aerodynamic effects and complex fluid behaviour in the micro- and milli-scales.
We are developing a virtual simulation of product printing, which helps us to determine the influence of factors that can affect the precision of the process, including angle of approach, rate of printhead rotation and required distances. Pilot trials are planned for testing different product requirements.
The collaboration is enabling the necessary early research to guide an exciting, ambitious and long-term research agenda focused on inkjet printing to create active devices and conductive tracks on advanced curved glass products.
Scaling-up customisation
It is one thing to establish new techniques in the lab, and quite another to scale them up for a manufacturing environment and for higher volume production. We focus on this need to understand scaling up, and collaborating with manufacturers including NSG Pilkington provides a way to test and analyse lab-based results in a production environment. Issues such as the impact of airflows on inkjet accuracy need to be understood both in the lab and in the factory for development of technologies which are both cutting edge and robust.
We anticipate that establishing and refining production techniques using advanced inkjet printing to be reliable in a factory environment will enable manufacturers to unlock affordable customisation in higher volume.
Nurturing innovation
NSG Pilkington has a dedicated R&D facility at its European Technical Centre in Lathom, Lancashire, where technicians have the freedom to test new ideas and look ahead to the next big trends that will shape the future of glass. Known as the Pilkington Innovation Incubator, the facility is a base where Pilkington’s staff can collaborate with any partner – from new tech start-ups, to larger businesses in other industries, to universities – in the pursuit of technological breakthroughs.
Dr Su Varma, Incubation Portfolio Manager R&D, has been at the forefront of building and growing the Innovation Incubator at Lathom. He explains:
“The incubator is designed to look further into the future – at what the medium and long term needs of the company may be in terms of technologies, and how these could give rise to new value-added products that take us into new markets. It’s about asking ‘Where are the opportunities in the future?’ Clearly, they tend to be outside of our normal glass world, which is why we link up with start-ups and other companies and Universities including Cambridge to find those early-stage innovations that we should be thinking about. Our collaboration with Ronan Daly’s centre at the Institute for Manufacturing, University of Cambridge, has directly helped us to explore cutting edge applications of inkjet technologies.
“Once we have set up a project through the incubator we will work to short timescales whereby we run the project for three months before inviting commercial colleagues to review it. If the commercial team believes there is a new, viable product in the offing, we will move it from the incubator into our normal, rigorous product development processes. We then fill the funnel mouth of the incubator with other new things and carry on.”