Using additive manufacturing beyond prototypes
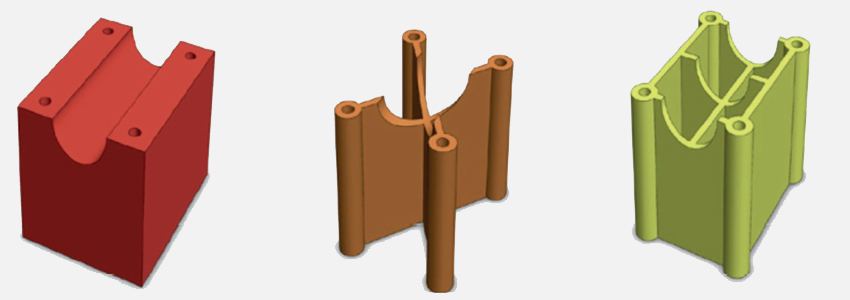
Additive manufacturing technologies have enabled significant changes to the way we design complex components and create early prototypes. But the uptake of these new production methods beyond prototyping and small-scale production remains slow. Dr James Moultrie considers how manufacturers could be using these new additive manufacturing technologies more effectively for series production of components.
Additive manufacturing (AM) has the potential to transform not just the way things are made but every aspect of how firms go about meeting their customers’ needs, whether through customisation, supply chain reconfiguration or wholesale business model innovation.
If AM is to move beyond prototyping and small-scale production and become mainstream, industrial designers need to have information on how to adapt component design principles for AM in series production, recognising that like all production processes, there are constraints as well as benefits.
We recently surveyed 110 product and industrial designers and design engineers from 25 countries. While 72% of respondents often or routinely use additive manufacturing for prototyping, more than 60% said they had never designed end-use components for production with AM.
What we discovered was that perceptions around cost and speed were holding manufacturers back from using AM for production.
Our survey respondents said that they would choose additive over conventional manufacturing processes when they were dealing with low volumes, complex shapes, shape manufacturability and customisation.
But when it comes to choosing additive manufacturing across production, they still have worries: the main reasons given were perceptions around cost and speed, concerns over repeatability and dimensional precision, and over the material properties of components.
The need for a different approach to design
Designers also noted that there is a lack of information to support design decision making. The information that exists focuses on ‘printability’, but printability in itself doesn’t guarantee parts which are cost-effective when produced in volume.
Whenever a designer designs a new component, they do so with an understanding of the limitations and requirements of the production process which they will be using.
For example, an injection-moulded part must have constant wall thickness, webs to support raised features and smooth transitions between surfaces.
These ‘rules’ and principles are well established and are readily available in textbooks and online sources. The same is true for the majority of production processes.
But where do designers look for information on how to design parts to take advantage of AM for series production?
The hype says that ‘anything can be produced’ and that ‘complexity is free’. Designers are suddenly freed from the shackles and constraints of conventional processes.
But is this true? Does AM provide limitless possibilities, or are there rules which can be applied to help designers make effective design decisions?
AM requires new ways of thinking, especially if designers are to progress from designing parts which are ‘printable’ towards parts which genuinely take advantage of AM as a production process.
To be able to exploit additive manufacturing capabilities for series production, designers, engineers and manufacturers need to have information on how its processes differ from other manufacturing processes and how they can be best deployed.
This means, in effect, going back to the drawing board – totally rethinking the concept of design for products made using AM.
Some new design principles
We have been working with industrial partners to develop a set of design guidelines that will help accelerate the uptake of AM as an economically viable production process and also help designers understand how they can take advantage of the capabilities of AM technologies.
This EPSRC-funded research project has been a collaboration between the University of Cambridge and Loughborough University.
While it is possible to use AM to produce almost any component you can imagine, if the aim is to produce parts efficiently – in 10 minutes rather than 10 hours – there are certain principles to follow.
As a result, we have begun to codify some of these design principles, which aim to help with the design of components which take better advantage of AM for series production.
Design for additive manufacturing: some new rules
- Use the least material possible
AM is often a slow process, and comparatively simple parts can take many hours to produce. The less material used, the less time taken. Therefore, shape optimisation to eliminate excess material might be beneficial, reducing time, resources and cost. - Don’t print air
As the print head moves around the build volume, time and therefore cost can be minimised if the shape is flat, has a low z-height and the shape isn’t an open or enclosed box. - Define and connect functional surfaces
Challenge conventional ways of thinking – it can be advantageous first to define the functional surfaces of a part and seek to join them in the most efficient way possible. - Minimise shape complexity
Despite the claims that anything can be printed with AM, complexity is expensive. The more changes of direction and greater distance the print head has to move, the longer a part typically takes to print. - Minimise infill
In certain AM processes, ‘solid’ shapes are not solid and comprise a surface that encases ‘infill’ (a honeycomb lattice) which holds the shape together. This infill is a form of ‘support structure’ and serves little functional purpose, while taking a long time to print. Thus, reducing or eliminating the need for infill can make parts more cost effective. This often results in parts that are more ‘shell’ like. - Minimise support material
Support material is generally indicative of a part that has not been optimised for AM production. - Enable nesting and tessellation in the build volume
Parts which ‘nest’ together – such as a stack of plastic cups with each nesting inside the next – enable multiple parts to be built simultaneously. Similarly, parts that tessellate allow for more components to be created at the same time. Again, this is more time and cost efficient.
Simple example of using AM to optimise a part for manufacturing – a) a simple device for holding a sensor on a machine; b) a range of alternative designs; and c) the most effective solution, which would save a significant amount of time and therefore cost, in a single build.
Putting the rules into practice
How might these rules work in practice? The CAD illustration above (part a) shows a simple device for holding a sensor on a machine.
The two red components are designed as you might imagine they could be for machining. They are ‘printable’, but they don’t take good advantage of AM as a production process.
We tried a range of alternative designs (as shown in part b), to see how they influenced the build time and cost. The results showed that the most effective solution (part c) can save a significant amount of time and therefore cost, in a single build.
More significantly, this shape tessellates, enabling multiple parts to be produced in a single setting.
It’s our hope that starting to codify AM design principles for production will facilitate designs which are cost, time and resource efficient. This, we hope, means AM might begin to be more routinely considered as a manufacturing choice for series production by industrial and product designers.
Design for assembly
One of the potential benefits of using additive manufacturing for series production is to reduce component count in assemblies. In addition to being interested in how we design parts for AM, at the Institute for Manufacturing (IfM) we have also done lots of work with companies on their design for assembly.
To support designers and manufacturers in developing competence in design for manufacturing assembly within their own organisations, we are working to disseminate our findings, including through an upcoming ‘Design for Assembly’ short course at the IfM on 14 May, as well as bespoke in-company workshops.